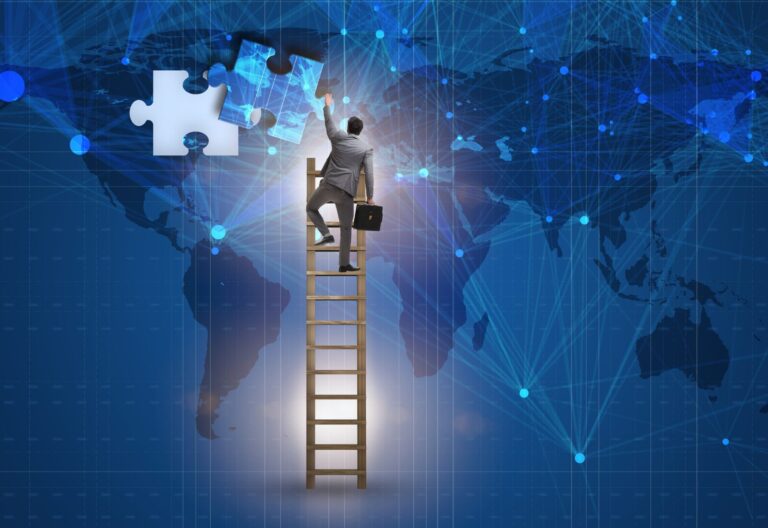
CFIUS Reporting Requirements for Non-U.S. Investors
CFIUS Reporting Requirements The Committee on Foreign Investment in the United States (CFIUS) is an interagency committee that reviews certain transactions involving foreign investment in the United States. Its role is to identify and address any national security risks that could arise from these potential investments. With increasing global tensions over technological competition and supply